Lateral & Mainline Pipe Sizing: How to Decipher & Test the Results
- "Pipe Charts"
- Example Test #1: Straight Run
- Example Test #2: Looped Run
- Downloadable Pipe Sizing Tests
If you're ever hesitant about the numbers Irrigation F/X is generating when you size your pipes, feel free to set your point of connection (POC) to Custom and then set your available flow and pressure to 0. Sizing the mainline will then show you negative numbers in the Critical Analysis, but they will be true demands of the system based on your setup.
From there, you should be able to cross-check the results on the critical station relatively quickly to verify that everything is calculating properly. For testing purposes against the book, rather than attempting to use an entire design, we recommend setting a "fake" test design that matches the book values exactly so you can get an apples-to-apples comparison (or as close as possible).
"Pipe Charts"
In the following tests, we'll refer to "pipe charts" in reference to the charts or tables that appear in the back of each manufacturer's product catalog, or from a specified pipe manufacturer's catalog you use for referencing the desired pipe class's friction loss, c-factor, and inner diameter. Examples:
Example Test #1: Straight Run
It's always a good idea to test a straight run as a confirmation that everything is sizing properly in the simplest scenario. Here's an example of a straight-run test we might run on an example system plan.
1. Place a pipe cap at one end of a 100-foot line, and set the flow demands to the proper amount for the pipe charts reading for the pipe class you're using.
In our example, we'll set the demand to 26 GPM based on a system using Schedule 40 PVC as the pipe class, which calls for a velocity of 4.20 fps.
2. Place a valve at the other end of the 100-foot line.
3. Pipe the cap and valve together with lateral pipe.
4. Label the valve with a valve callout.
5. Use our Size Lateral Pipe tool to size the valve. Set the velocity to 4.20 fps to match the reading in the pipe charts.
You should immediately see that the pipe was sized to the same size as shown in the pipe charts. However, we are less concerned about this and want to focus on the friction loss that is being generated.
6. Open our Edit Equipment tool and click on the valve.
Click the Analysis button.
Take note of the Friction Loss entry you see in the Station Analysis dialog box.
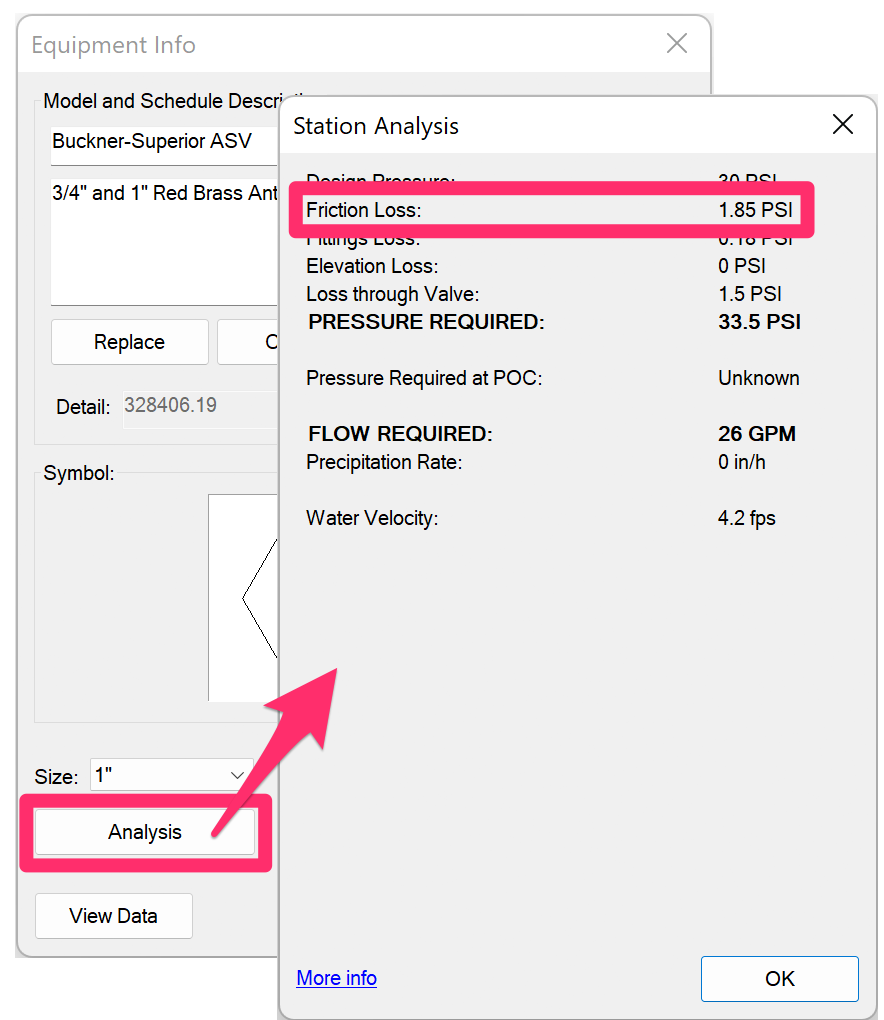
7. Run your numbers through the Hazen-Williams formula. The result should be an almost exact match with the Friction Loss reading you noted in the Station Analysis dialog box above, all depending on how many decimals were used in rounding.
In this example, we calculated 1.86 psi loss, where the system generated 1.85 psi loss, which should be completely acceptable.
Keep in mind that if you're seeing a wildly different result, you might have a value set differently from what the system is using. This could include pipe class, inner diameter of pipe, flow used, c factor, or simply improper order of operations.
Example Test #2: Looped Run
Once we've confirmed that everything is indeed sizing properly, we'll move on to a test that includes the complexity of a looped system.
In this example, we'll apply a simple test case of a looped system using the same cap values as those used in our straight-line test above. If this passes, we know the same logic would be applied to your actual design.
Keep in mind that with this test, Irrigation F/X will apply a more thorough breakdown of how the water needs to be split based on path lengths, then apply the worst-case scenario/demand for the final numbers, so it will not be just a simple "split the flow and pressure evenly" type of logic.
Here is a breakdown of what the system is doing (so you can test the same thing manually):
• Generating the path lengths and percentages
Keep in mind that the more loops introduced to a plan, the more path options each valve will have, making the analysis of worst-case scenario that much more complicated. (Our example will include two paths: a short route (Path A = 200') and a long route (Path B = 400').)
- Take note of the total path length (Sum of Path A & B = 600').
- Divide the total path length (600') into Path A (200/600 = .3333%) & Path B (400/600 = .6667%).
This calculation is essentially telling us in an inverted way that Path B will receive 33% of the water and Path A will receive 67%, since the water will reach the shorter path first and will therefore take longer to travel through the longer path.
• Splitting the flows per path
- Take the Total Flow (26 GPM) and multiply each path by the proper % (Path A: 26 * .6667 = 17.3342 GPM) (Path B: 26 * .3333 = 8.6658 GPM)
Now we can size the pipes based on the given flows for each path, again using the Hazen-Williams equation linked above. Because we have a slightly more complex example here, we cannot forget that the friction loss calculation is based on 100', so you will need to multiply your result by the path length and divide by 100.
*Example:
Path A = 200'
- Path A head loss (4.33795): = .2083(100/c factor(150))^1.852 (17.3342)^1.852/(inner diameter of pipe that closest matches the velocity you wish to achieve)^4.8655
- Path A friction loss (1.8783): = 4.33795 * .433
- Friction loss for total path (3.7566): = (1.8783 * 200) / 100
Path B = 300'
- Path B head loss (4.6664): =.2083(100/c factor(150))^1.852 (8.6658)^1.852/(inner diameter of pipe that closest matches the velocity you wish to achieve)^4.8655
- Path B friction loss (2.0205): =4.6664 * .433
- Friction loss for total path (6.0616): =(2.0205 * 300) / 100
Path A & B (where loop converges back to POC) = 100'
- Path B head loss (1.8607): =.2083(100/c factor(150))^1.852 (26)^1.852/(inner diameter of pipe that closest matches the velocity you wish to achieve)^4.8655 = 4.2973
- Path B friction loss (1.8607): = 4.2973 * .433
- Friction loss for total path (1.8607): =1.8607 * 100 / 100
• Final assessment
Irrigation F/X will now determine with each path + combined path losses, which path has the highest pressure loss to account for, and will list this in the Critical Analysis.
Path A: 3.7566 + 1.8607 = 5.6173 psi loss
OR
Path B: 6.0616 + 1.8607 = 7.9223 psi loss **Winner!**
Checking the Critical Analysis should line up very close to your manual test, which, in our case, it does.
Downloadable Pipe Sizing Tests
We've created both pipe sizing tests described above in a downloadable DWG file. Use the link below to download the pipe sizing test.
The download will result in a file named Sizing test.zip in the location where you downloaded the link. Double-click the downloaded file to unzip it, then open the sizing test.dwg file within the resulting folder to run the test.